The humble toothbrush has a long history. It dates back as far as 3500BC and has evolved over time into the
electric toothbrush many of us use today. The manual brush still exists as does the fundamental principle why we use them.
Having considered the history, have you ever wondered how a toothbrush, be that a manual or electric one is actually made?
We wondered this and have done some research to establish just how toothbrushes are manufactured today.
Naturally the process may differ from brand to brand, and if the toothbrush is electric or not, but the key stages of production are similar.
Years ago a brush will have been made by hand, but no longer. Sophisticated machinery allows them to be produced quickly and cost-effectively.
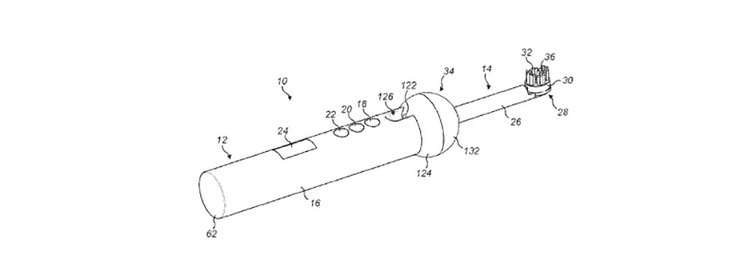
Design
The initial stage before manufacturing is to actually design the electric toothbrush.
Electric toothbrush manufacturers and product designers will work together to create a toothbrush.
The design of the electric toothbrush will be influenced by a number of factors, such as the intended audience, for example adults or children. It may be influenced by research be that medical or consumer trends that could affect the shape, colour and angle of the brush head.
A whole host of different considerations are made during the design process to come up with a product that meets the brands needs, but is also possible to produce.
This may take a number or attempts to get something that is right and appropriate.
The design and production elements all affect the cost consumers pay. More technically advanced or specialised products will often result in a higher production and resale cost.
Prototypes or samples are often made to test and check certain elements of the design and production process, before tooling up for mass production. It is at this stage changes might be made if issues are found that were not apparent from the initial design and concept stages. Prototypes are tweaked until all parties are satisfied.
Once agreements are made, the production line will be configured for producing this product. This includes creating appropriate molds and changes to equipment that are needed in the manufacturing process.
Some brands will produce the electric toothbrush themselves, whilst others may outsource the production to another company. In some instances, brands buy an ‘off the shelf’ design and customise it with their logo, packaging etc.
Moulding the handles
One of the first stages is actually making the brush handle.
Plastic pellets or granules are placed into an injection moulding machine, which heats the pellets until they melt. Once a hot liquid a rotating screw or plunger forces the plastic into the mold.
The moulds are often for the entire handle of the brush, including the small holes in which the bristles will later be fitted. These holes are called cores.
The single piece moulding process makes normally for a stronger toothbrush.
For an electric toothbrush the brush head is usually made separately (using a similar process) and the handle, larger and hollow for a motor and battery to be fitted within.
Pressure often in the form or gas or air is then applied inside the mould until the plastic has cooled and formed into the final shape.
Once complete small pins push the handle out of the mould and into the filling machine.
It is not uncommon at this stage for computers and sensors to check each brush handle to make sure it meets the specifications desired and no faults have occurred during the moulding process.
The filling machine
Typically made from nylon the bristles are positioned into the core of the handle or brush and secured with tiny metal staples/straps that stop them coming out.
Depending on the design of the brush head, bristles may be thicker or thinner as well as softer or firmer, with a combination of such being used on some brush heads.
Bristles may also be different colours for design purposes or for functional reasons.
Many brushes now have fading indicator bristles, that discolour over time to act as a reminder to change brush heads regularly.
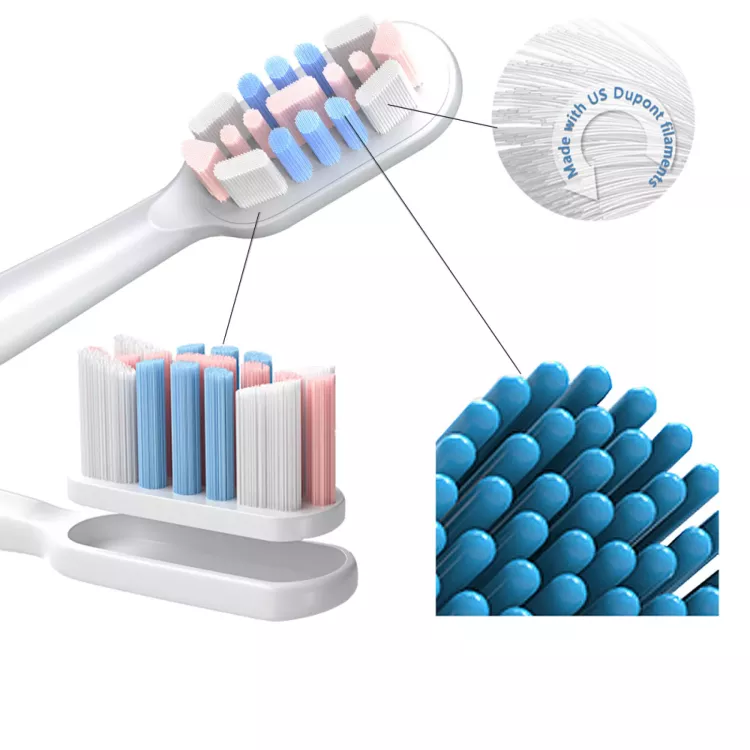
Once the bristles are in place, they are normally a bit rough. They need to be cut and shaped to the manufacturers specification.
A computer guided machine will guide a sharp blade, that will slice the bristles to the correct length and shape for the brush being made.
Bristles are often blunted as part of this process to remove sharp edges. In some instances the bristles are cut or specifically designed to have a contour to the tip to help in the brushing and cleaning process. Rounded bristles tend to be softest and most comfortable on the teeth and gums.
Sterilising the brush
Brush heads are passed through a UV light to kill off any germs and bacteria, making them safe for use by you and me.
Inserting the motor, battery & gearing for an electric toothbrush
In the case of manufacturing an electric toothbrush, a motor, gearing system and battery are connected together, checked to see if they function and then inserted inside the hollow brush handle casing. The components are then sealed inside with a plastic top/cap, that forms the base of the brush handle.
Packaging the toothbrushes
The toothbrush has now been produced. It then goes for packing.
In the case of a manual toothbrush, this is often a plastic and/or cardboard container. This protects the brush a little and keeps it free from germs.
The packaging will include all the information about the product that you and I as consumers can see and read when looking at them on the shop shelves.
An electric toothbrush is normally packaged in a larger box, with the appropriate brush head and in many instances a number of other accessories that have been manufactured either on the same site or elsewhere. They are brought together into one box.
The individual brushes are grouped into larger boxes for shipping and distribution in stores.
Testing
This will vary from one manufacturer to another, but big brands will often take a batch of brushes, put them through a number of rigorous tests. Providing the samples pass this, they are cleared for shipping and sale.
As a professional manufacturer of electric toothbrush and oral irrigator / water flosser, Shenzhen Relish provides various types of electric toothbrush wholesale and OEM customized services. You can also wholesale water flosser from Relish at factory price. We can provide you highly competitive prices and look forward to working with you.